Here's a detailed guide on assessing the quality of materials from the Chinese furniture manufacturer, like OPPEIN, especially when considering custom kitchen cabinets, wardrobes and other furniture.
1. Understanding the different types of materials used
Begin by becoming familiar with the different types of materials commonly used in the manufacturing of furniture. For example solid wood, plywood, MDF (medium-density fiberboard) particleboard, and laminate are prevalent selections. Each one is distinct and has its own distinct characteristics as well as advantages and disadvantages. Solid woods are typically the strongest and most attractive and attractive, whereas engineered materials like MDF are generally more affordable and adaptable. It is possible to make a well-informed choice based on what you look at when comparing.
2. Verify the Certifications
Keep an eye out for certifications to indicate quality and safety standards. Certifications like CARB compliance (California Air Resources Board) that indicate the emission standards for formaldehyde in wood products, or ISO certifications that signify manufacturing management quality systems, are good indicators that a manufacturer is committed to producing high-quality and safe products. These certifications are usually used to ensure that the materials used do not contain any harmful chemicals or are in compliance with international standards.
3. The wood grades include:
Ask about the grade of the wood if the company makes use of solid hardwood. The appearance, durability and intended usage of wood are all factors that go into grading it. The higher grades (e.g. A and B grades), will have less knots and defects. This leads to an attractive finish. Knowing the wood grade will assist you in determining the durability and the quality of furniture.
4. Inspect Surface Finishes:
The quality of surface finishes will significantly impact the longevity and look of furniture. The surface finish should be even and smooth and resist scratches, stains and moisture. You can test the appearance and feel of various finishes by requesting samples. Also, ask about how they are applied (e.g. several coats or curing time) to make sure that they meet your requirements.
5. Check Hardware Components
The hardware used in furniture (such as hinges, drawer slides or hinges) slides) plays an important role in the overall quality of the furniture. Material and construction should be taken into consideration. Hardware that is of high-quality will feel solid and run smoothly, as well as endure wear. Pick brands or specifications with the reputation of reliability, such soft-close mechanisms on drawers as well as on doors.
6. Inquire About Sourcing and Sustainability:
Investigate where and how the manufacturer sources its products. Sustainable practices in sourcing not only benefit the environment but can show a firm's dedication to quality. Find out the source and management of the forest that the wood was obtained. In order to protect their reputation, those who put a premium on sustainability often raise standards for quality.
7. Review Samples of Product:
Request samples of furniture or the prototypes you're interested in. This allows you to see the quality of materials and workmanship in the flesh. Take note of the way they feel, how much weight and how they are built. The material should be solid and sturdy with no signs of weakness or instabilities.
8. What Test Procedures to Have Questions?
Inquire if the manufacturer conducts material testing to assess durability and performance. The most reliable manufacturers often conduct tests on wear resistance. Knowing how they test their products can give you the confidence to purchase their products since it shows their commitment towards quality control.
9. Examine the Transparency of the manufacturer:
A trustworthy manufacturer should be transparent and open about their products and processes. They should be able to provide information in detail about their raw materials, practices for sourcing and certifications. It could be a sign of poor quality when the manufacturer is not willing to share the information.
10. Take a look at the reviews of customers and Feedback:
Check out reviews and testimonials from customers who have been through the process. Reviews on the durability, quality of materials, and overall customer satisfaction are extremely useful in determining what you can expect. To assess the reputation of the manufacturer, pay attention to frequent themes like complaints or praise about the material's quality.
In the end, evaluating the quality of materials from a Chinese furniture maker such as OPPEIN is a careful evaluation of a variety of factors, such as the types of materials, certifications, and customer feedback. By following these detailed suggestions, you'll be able to make an informed choice and be sure that the furniture you select is in line with your standards of quality and expectations. See the top rated OPPEIN for website recommendations including shaker style kitchen cabinets, best kitchen cabinets, armoire with drawers, melamine cabinet, kitchen furniture, types of kitchen units, clothes armoire wardrobe, rustic cabinets, white kitchen cabinets ideas, kitchen cupboard styles and more.

Top 10 Tips On Assessing The Lead Times And Capacity To Produce Of A Chinese Furniture Manufacturer
Here is a guide that will assist you in assessing the capacity for production and lead times of a Chinese manufacturer such as OPPEIN. This article will be particularly useful for custom furniture like cabinets for kitchens, wardrobes and many more.
1. We invite you to request detailed production schedules.
Ask the manufacturer to supply you with a detailed production schedule. This should include timelines for each phase of manufacturing, from raw material sourcing to the final assembly and delivery. Understanding the timeline helps determine if their production capacity aligns with your project deadlines in order to ensure they meet your specific requirements.
2. Inquire About Standard Lead Times:
Ask the manufacturer what their average lead-times for different types furniture. The lead times for furniture can differ greatly based on product complexity, customization options, and the volume of orders. Knowing the average lead times for the particular items you're interested in will allow you to gauge the ability of these products to complete your orders promptly.
3. Examine the ability to handle large orders:
Assess the ability of the manufacturer to handle large orders, especially in the case of large-scale projects like outfitting the entire hotel or collection of apartments. Ask about the manufacturer's maximum production capacity per product line. Additionally, you should determine whether it is able to scale production in times of peak demand.
4. Understanding the effects of the customization of lead times
Ask the manufacturer about their approach to this. Customizations may extend lead times. Consider how much extra time is typically required for custom orders as compared to standard products. Transparency is shown when a company clearly explains the impact of customization on lead time.
5. Evaluation of Flexible Production Scheduling
Find out if the manufacturer is flexible when it comes to the dates of production changes. The timeframes for projects can be altered at any time and the company has to be able to adapt to these adjustments. A manufacturer who can adapt to changes in lead times or prioritize urgent orders is more likely to be able to meet your evolving needs effectively.
6. Assess the efficiency of your workflows and processes:
Examine the effectiveness of the production process. Find out about the workflow of the company, automation and lean manufacturing methods. A company that uses efficient processes and the latest technologies is likely to have shorter lead times and a greater production capacity, which will enhance your overall experience.
7. Make sure you have a backup capacity.
In the event of an unexpected issue such as equipment malfunction or supply chain disruptions, it is important to have a contingency plan in place. Ask whether they have a an alternative production capacity or suppliers for materials. A company with solid contingency plans is better prepared to handle unforeseen challenges without significantly impacting lead times.
Review Performance Metrics for the Past:
Ask the manufacturer for information on their performance over time in terms of lead times and production capacity. Included in this are data such as the average lead times across all product categories, the rate of on-time deliveries, and changes in capacity of production. It is possible to gain insights through analyzing this information.
9. Examine Communication During Production:
Effective communication is essential during the entire production process. Ask how the company keeps customers informed on the progress of their orders. Communication from a manufacturer that is open is a sign of commitment to customer service, and helps you control your expectations throughout the entire project.
10. You may also request reviews from clients who have previously worked with you.
Request references from customers who were involved in similar projects in the same way with the producer. Contact these customers to ask about their experiences with regards to timelines and production capacities. Positive feedback is an excellent method to assess the commitment of a business and its ability.
To conclude, evaluating the lead times and capacity of the capacity of a Chinese manufacturer, such as OPPEIN is a comprehensive review of the production schedules, the flexibility of processes, their efficiency as well as feedback from customers. You can be sure that the company meets your needs and timeframes by following these suggestions. Take a look at the top rated wardrobe manufacturers for website examples including high gloss kitchen cupboards, design for cabinet for kitchen, cabinets modern kitchen, order kitchen cabinets, europe kitchen cabinets, cheap cabinets, affordable kitchen cabinets, custom wardrobe closet, kitchen units designs, contemporary kitchen and more.
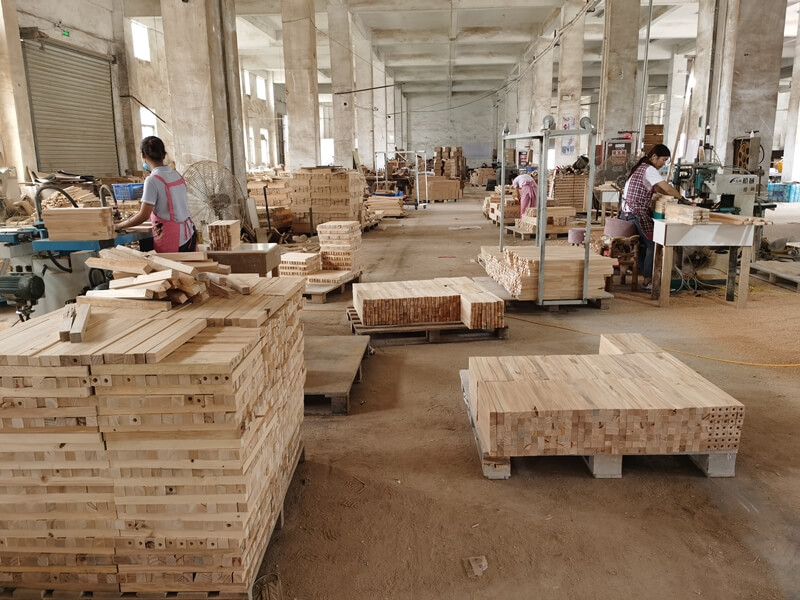